The Future Of Industrial Maintenance Is Predictive
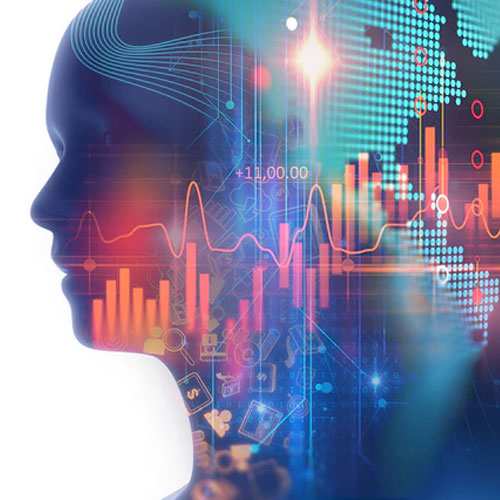
Industry 4.0 and IoT are key elements of the digital revolution and there is need to modernize the maintenance with IoT and we can call it “Maintenance 4.0” ,it provides a unique opportunity for industrial customers and partners by, using IoT to connect industrial machinery, including legacy tools, automating maintenance workflows through predictive analytics by minimizing downtime before warnings sound and at the same time one can visualizing performance data and production status. Whereas, predictive maintenance lets you monitor equipment health to avoid future failures during operation. It uses predictive algorithms with data from equipment sensors to estimate when your equipment will fail. Digitalization is advancing at a rapid pace, and innovative pioneers are successfully defining and implementing digital agendas.
One of the main challenges in implementing IoT technology is data security. With all of those devices and equipment connecting to the internet, your network is more vulnerable to attack. Hackers are known to be creative when they manage to break into a system; they may use a piece of connected equipment to gain access to private data on your network or wreak havoc on building automation protocols just for fun. The future is bright for the IoT. As costs come down, it will become easier to implement, and more companies will take advantage of the benefits it provides. As such, maintenance technicians will need to become more proficient in turning data into actionable insights, in addition to their current skills. Industry 4.0 and IoT, defined as intelligent, interconnected equipment and products autonomously communicating and optimizing along the entire value chain, are key elements of this digital revolution.
Going forward, the IoT will become the norm, instead of the exception. As companies find ways to overcome cost, connectivity, and security barriers and gradually update their maintenance systems, it will be easier to implement the IoT in commercial buildings of all types.
The Internet of Things (IoT) has drastically transformed the manufacturing and field service business. With it, companies are no longer limited to managing the maintenance of production assets based on equipment age or usage to stay ahead of costly failures. Resulted increases equipment uptime ,Improve service delivery and it creates new service revenue streams – Produces recurring revenue streams by gathering and analyzing data that complements predictive maintenance, and presents opportunities to monetize services. At the same time, the global IoT professional service market is expected to witness the rise due to the growing demand for real-time insights, productivity, and efficiency in an organization and the need for asset monitoring and utility maintenance in various industries. The IoT professional service includes a portfolio of services and capabilities to take the complexity out of IoT, offer the right consultancy for the business and help bring the suitable IoT mix product. Data-driven customer insights and real-time information is the most important customer service and experience.
Predictive maintenance brings a more data-driven approach to industrial-maintenance programs. It uses predictive analytics and machine-learning algorithms based on historical and real-time data to identify specific issues on the horizon. Often these issues won’t be showing any physical signs of degradation – even a sharp human eye or an intuitive and well-trained maintenance technician wouldn’t be able to catch them. In addition to helping prevent downtime, a predictive-maintenance approach can better identify true maintenance needs. This can help make sure you’re targeting maintenance activities and maintenance dollars where they’re needed most.
See What’s Next in Tech With the Fast Forward Newsletter
Tweets From @varindiamag
Nothing to see here - yet
When they Tweet, their Tweets will show up here.