Industry edge 4.0
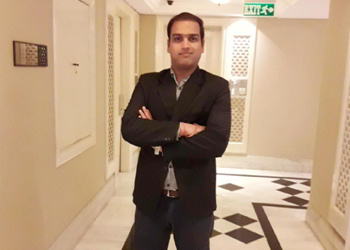
Industry 4.0 is the fourth industrial revolution, turning factories into smart factories, filled with sensors that collect data to intelligently optimize operations, driving more and more automations. Factories are becoming smarter, automated, flexible and more efficient using new technologies. Data centre technologies and digital tools playing a vital role. Instead of simple machines, aim here is to create cyber physical system- network of collected machines that collect massive amount of data through sensors, act for new level of insight & perception. Factory floors are managed with mission critical IT, housed in a specialized data centre, inside the factory or outside (cloud) facilities. Factory IT has to be rugged, immune to the danger of manufacturing environment, includes dust, pollution, vibration and electromagnetic pulses. Networking is the real key. This requires an Industrial internet; Information technology (IT) merges with Operational technology (OT) - branch of the organisation handling mechanical devices and physical infrastructure. This would help to mitigation security risk from networked mechanical equipment’s- which are emerging as a serious concern. At the same, OT manager’s experience IT benefits too. In manufacturing, IT customers strongest than OT customers.
# R1.0 (Steam and Water) - In the 18th/19th centuries, factories emerged with steam and water power, creating the first wave of automation.
# R2.0 (Electricity) - At the end of 19th century, electricity arrived as a more flexible power source.
# R3.0 (Computer) - In the last 20th century, numerically-controlled machines such as lathes, CAD/CAM etc. and robot arms began working with data from computer aided design files.
# R4.0 (Full Digitalization) - Beginning this century, all process are automated, connected, factories are instrumented with sensors; more flexible and efficient.
The data lifecycle begins on the factory floor, with industrial Internet of things sensors capturing readings from machines involved with the production process. Real time data could be captured from Distributed control systems, manufacturing execution systems (MES), Asset management systems (AMS) etc. With edge data centre, run own private cloud solution for the necessary processing (and protections). Effective data journey is about mixing the real time electronics of the machines on the factory floor with response of edge facilities, and big data insights that require massive computing power, can be accessed via cloud run. It’s clear that digital infrastructure is bringing a whole new approach to manufacturing while, at the same time, the industrial vertical is demanding new capabilities from sensors, edge data centres and micro-facilities.
Sourabh Tiwari
CIO/IT-Head - Overseas Infrastructure Alliance (India)
See What’s Next in Tech With the Fast Forward Newsletter
Tweets From @varindiamag
Nothing to see here - yet
When they Tweet, their Tweets will show up here.